Based on the success for building 8-10m class telescopes by the International astronomical researchers, the constructions of 30m class Extremely Large optical/infrared Telescopes (ELTs) have been started.
The light collection area of one 30m telescope is almost the same as the sum of all the existing 8-10 m class telescopes. The primary mirror of the ELT is generally composed by hundreds pieces of off-axis aspheric segment mirror with 1-2m diameter. Because of the large diameter and the high precision requirement of the segments, the fabrication technique is a very important issue that should be researched to build the ELT.
The classical Stressed Mirror (SM) technique developed in the fabrication procedure of 10m telescopes (such as KECK and GTC) can only satisfy the efficiency requirement of 10m class telescope (about 30 pieces of segments in the primary mirror). However, the segments number of the ELT is more than 10 times of the 10m telescope, so the fabrication speed of the classical SM technique is too slow. Several foreign organizations focused on the problem and made some improvements for SM technique in respects of fabrication precision and efficiency, but there is not the revolution for the technique.
Nanjing Institute of Astronomical and Optics Technology is the first organization to propose the concept of combining the SM technique and the Continuous Polishing (CP) technique into the Stressed Mirror Continuous Polishing (SMCP) technique, and carried out the relative research supported by the National Natural Science Foundation.
Using the SM technique, varies type of off-axis aspheric mirrors in the primary mirror can be fabricated evading the high frequency error which will generate in the traditional small tool polishing; On the other hand, several pieces of segments can be polished simultaneously due to the CP technique, therefore the efficiency is improved greatly. As the result, the SMCP is very suitable for the segments fabrication of the ELT with the requirement of high precision and large amount.
Based on the designed parameters of China Future Giant Telescope (CFGT) we polished an off-axis segment with the radius of curvature of 21.6m, the off-axis distance of 3.6m and the segment diameter of 330mm in the experiment. The polishing result is good shown in Figure 1, where it can be seen that after about 40 hours of SMCP, the surface shape error tends to reduced to 0.327λ (RMS value, and the wavelength λ is equal to 0.6328μm).Finally the surface error RMS is better than 0.02λ after the figuring and cutting to hexagon.
Our technique attracted the attention of the Thirty Meters Telescope (TMT) project in the United States. With the organization of National Astronomical Observatory, our institute started the cooperation with TMT project to polish the off-axis aspheric segments. The SMCP fabrication and measurement fixtures of 1m class segments were developed so that the segments can be polished on a 3.6m CP machine.
At the end of 2014, two segments with the diameter of 1.1m are completed, which are the scale-down versions of the 1.5m TMT segments. Their off axis distance are 8m and 12m respectively, which belong to the different regions in the TMT primary mirrors. Both segments can satisfy the requirements of TMT project after the fast fabrication procedure of the SMCP (shown in Figure 2).On the assessment meeting in March 2015, this research result was accepted by the TMT project group (see Figure 3).
Fabrication of the off-axis aspherical segments with high precision is a very important technique for building the ELT. Therefore, the SMCP technique is valuable for the development of the optical telescope in the next generation. Besides, it can also be applied in the industry with the mass production requirement of the aspherical segments.
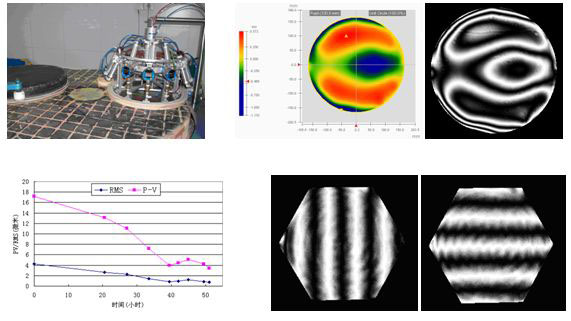
Figure 1. The SMCP device for the 330mm segment polishing (left up); The convergence curve of SMCP (left bottom); The surface shape error of the segment after SMCP (right up); The interferometry fringes of the surface error after final figuring and cutting to hexagon (right bottom) .
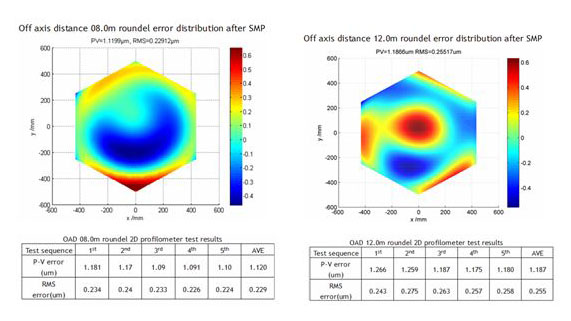
Figure 2. The polishing result of two off-axis segments with the off-axis distance of 8m and 12m respectively.
Figure 3 is picked from Progress Assessment Report.
(Information Source: Nanjing Institute of Astronomical Optics & Technology, CAS)